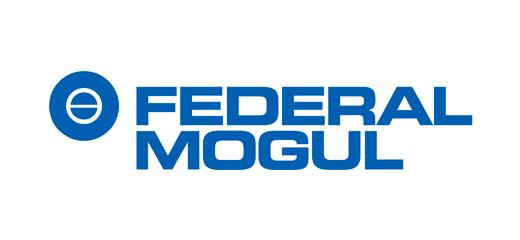
Success Story of Automotive Industry
Advanced Production Planning and Detailed Scheduling
Formed in 1998 through the combination of global industry and technology with Turkish capital, Federal-Mogul Turkey has become one of the most important facilities in the world in terms of capacity and technology in the field of motor component production. With its continuous investments, Federal-Mogul brings the latest technology in motor parts production to Turkey and increases its capacity, employment, and technological capabilities every year.
Why was the project needed?
Dinçer Koruk, Logistics and Planning Manager at Federal Mogul, explains why they started the project: "Our production consists of many integrated processes. It is crucial to control production capacity adequacy according to incoming orders. However, planning capacity according to all processes and constraints of production was taking a long time. When we dreamed of this project, our first goal was to prepare a production plan in a shorter time and to react faster to production variations. Our second goal was to optimize performance metrics such as order preparation times, on-time delivery rates, and total machine setup times. In pursuit of these goals, we sought planning software to assist us. During the period when we prepared plans with the help of SAP and Excel, each process step was planned separately without considering how they affected each other. Therefore, while we thought we were planning one process very well, we were actually creating great inefficiencies in other processes. However, we couldn't see these inefficiencies before they happened in real life, so we couldn't take precautions. This situation was causing many problems for us, such as increased intermediate stock levels, low on-time delivery performance, inefficient use of resource capacity, and inability to provide error-free delivery dates to customers."
We integrated Asprova with both our ERP and MES infrastructure.
Thanks to Asprova, all our processes became synchronously planned. By identifying capacity shortages or excesses in which process and machine at the beginning of the planning period, we were able to prevent both overtime and order delays with workforce shifting scenarios.
Dinçer Koruk
Federal Mogul, Logistics and Planning Manager
What solution was provided?
We wanted an innovative approach on behalf of our company and decided to use planning software outside of ERP. We realized that highly qualified and equipped consultancy services were needed for such a project to be successful. During our research, we chose Dijitalis, which offered us very flexible and rapid solutions. From the first stage, we trusted that they would show the same attention to us during the project, provide quick solutions to possible problems, and guide us with their experience.
The biggest reasons we chose Asprova as the software were its high number of active users, its service in many different industries, especially its serious references in the automotive sector, its ability to be customized for the user, and its very fast operation. We saw that Asprova would improve important production KPIs for us shortly, which would contribute financially to our company. It was clear from the beginning that the ROI of the project would be high.
What was achieved at the end of the project?
All our production know-how, that is, all production rules and constraints, were defined in detail within Asprova. Process planning became independent of the person. We established our own standard by planning according to the same rules and constraints at all times and under all conditions. With this standardization, we eliminated a significant problem we had experienced in the past. These problems included planning different products that used the same substructure on different production machines at the same time, planning incompatible products for that machine according to its capabilities, and not being able to plan the order as a whole across all processes.
With Asprova, we reduced our machine setup times by 10% and increased our OEE rates by 8%. Our average order preparation time was shortened by about 3 days on average, and our intermediate stocks decreased by 15-20%. Starting to work with fewer stocks, we saved space in production. By integrating planned maintenance into the production plan, we gained vital capabilities such as foreseeing when the order would actually be completed, easily tracking past and future performance of production, and deciding on overtime needs during planning rather than at the last minute. With high scheduling speed, we became able to quickly test different "What-If" scenarios, which gave us the power to shed light on and manage the future.
What are your recommendations for other companies?
When starting such a project, it is beneficial to define all production constraints and rules very well and to work on and introduce detailed functional functions. You can clearly observe the tangible benefits of advanced planning and scheduling software after the project is completed.
We showed that it is possible to reduce production costs and increase production volumes by better planning existing resources without making new capacity investments. We owe our gratitude to the Dijitalis team for showing us this.
With the project we carried out with Dijitalis;
- We reduced machine setups by 10%,
- We can now do detailed scheduling for 60 days while we used to do it for 5 days,
- Our production planning process, which used to take 1 day manually, is now reduced to 2 minutes,
- By shifting manpower from low workload processes to processes requiring overtime, we reduced overtime by 80%.
- We achieved a 15-20% reduction in intermediate stock levels.
- Our capacity utilization rate increased by 8%.
- Our average order completion time decreased by 3 days.
- Our raw material stock levels decreased by nearly 10%.
Dinçer Koruk
Federal Mogul, Logistics and Planning Manager