The Future of Manufacturing: Robotic Automation
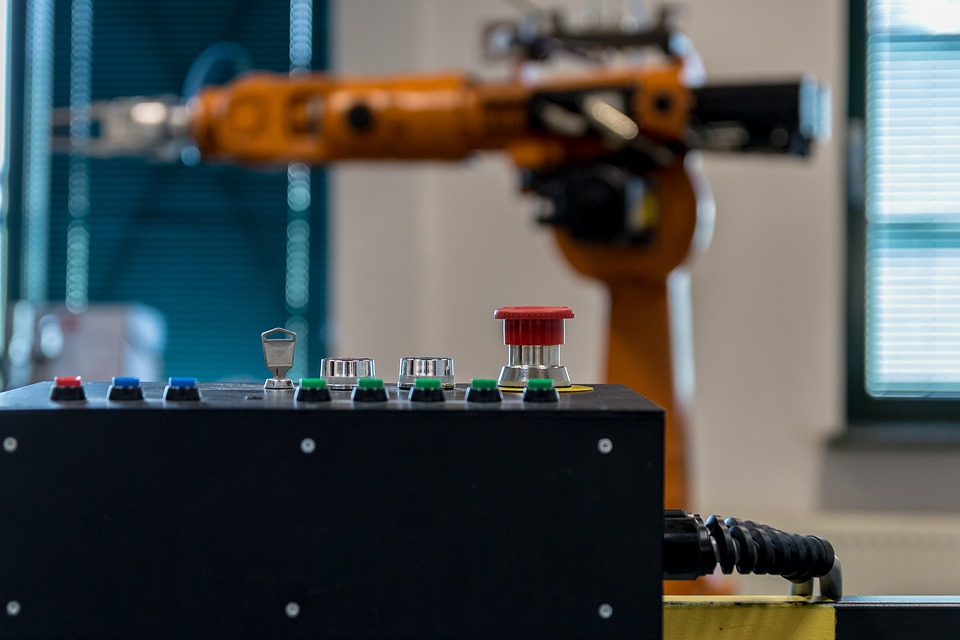
The Fourth Industrial Revolution, or more popularly known as Industry 4.0, has increasingly impacted the technology in the business sphere every passing day. This has heightened communication among machines, systems, and humans, digitized production processes, and affected all companies, big or small. The concept of Industry 4.0 encompasses:
- Industrial communication used in factory automation,
- Advancements in control systems, development of image processing and computer vision technologies,
- Advancement of artificial intelligence algorithms, and
- The utilization of data collection systems in nearly all manufacturing technologies.
The concept of Industry 4.0 has been rapidly embraced. The use of technologically advanced equipment in the manufacturing sector is increasing steadily. Industrial robots, which have begun to be used in this sector, constitute some of its most important technologies. Progress in human-robot interaction has been achieved through technological advancements in industrial robotic systems. These robotic systems engage in active and passive collaboration with humans, thereby contributing to factory automation. The utilization of human-robot interfaces in flexible manufacturing systems has ensured that precision and safety measures are brought up to standards.
New industrial technologies are one of the major factors increasing production efficiency in complex manufacturing processes. Among the technologies used to maximize flexibility and efficiency, digital transformation and digital twins stand out. Virtual Commissioning’s Power
By employing comprehensive digital twin technology in your production process:
- You can significantly reduce the lead times for the implementation of new machinery,
- New processes, and
- New products.
For example, consider setting up a new CNC flexible manufacturing cell. By synchronously working, the design and installation processes of machine and robotic material handling systems in this cell can be verified before the digital twin of the production line is created. This means that problems are solved, potential errors are prevented, and a faster control process is ensured before moving into mass production. Through digital twin-PLC integration, the commissioning of automation-intensive production lines may take less time. Virtual commissioning, which forms the critical foundation of an efficient production environment, enables a continuous cycle of innovation while optimizing the entire facility.
Virtual commissioning ensures not only software controls are tested but also the efficiency of control strategies. When factories embark on the journey of robotic automation, it’s essential to create an environment where such experiments can be conducted cost-effectively and risk-free. In such a virtual experimental environment, future production technologies can be designed to deliver maximum efficiency from today.
Simulate Before Deciding!
To minimize risks during the update or renewal of an existing system, the best decision is to simulate new processes. New processes may not function as expected in the factory, and plans may yield unexpected results. Therefore, it’s necessary to calculate every detail of the investment in automation and eliminate risks. In this digitalized process, the point where digital twin technology comes into play is precisely here. Seeing how new equipment will function in the production process and comprehensively examining operations within a factory prevent investment loss.
The increasingly widespread use of Internet of Things (IoT) devices and sensors is crucial for bridging the gap between digital twins and physical processes. IoT projects are often placed on production equipment and evaluate the performance of that machine internally. However, what’s essential for a factory is how the vast amount of data collected from machines can be utilized to maximize the performance of the entire system. This is precisely the problem simulation primarily solves.
Optimizing Factory Logistics with Autonomous Robots
The foundation of a flexible manufacturing system relies on support from simulation, virtual commissioning, and advanced robotic tools. Automatic Guided Vehicles (AGVs) and Autonomous Mobile Robots (AMRs) are examples of such tools. While conveyor systems used extensively in manufacturing logistics essentially move a product from point A to point B, they are static in nature, no matter how efficient and economical they are. In contrast, AGVs and AMRs begin moving material to their new locations immediately, adapting their routes as per changing needs. Time-saving is crucial for a flexible production system.
To explain this further, consider a factory producing a product in two different versions. In the first version, assembly cannot continue until bolts are tightened. In the second version, bolts can be tightened after assembly is complete. In the factory with static conveyors, where the flow of materials is determined by the product being manufactured, only one conveyor flows at a time while the other remains idle. However, in a facility where an AGV or AMR fleet transports materials and workpieces, products can be dynamically rerouted, and the production sequence can be rearranged according to the available machine. Or, when dealing with highly customized consumer products, components can be directed to the best machine for the next operation.
Benefit from Future Robot Technology Today
To achieve this, it’s essential to ensure that the mentioned technologies work seamlessly together. Pre-simulating using a digital twin is necessary to ensure that the production system is correctly designed. Validating robotic automation systems using the virtual commissioning method is crucial for approving the process.
We are experienced in creating the digital twin of robotic automation systems. We explain our sample applications on our YouTube channel. To learn more, you can watch our videos about digital twins on our channel here.