5 Strategies to Optimize Your Production Planning and Scheduling
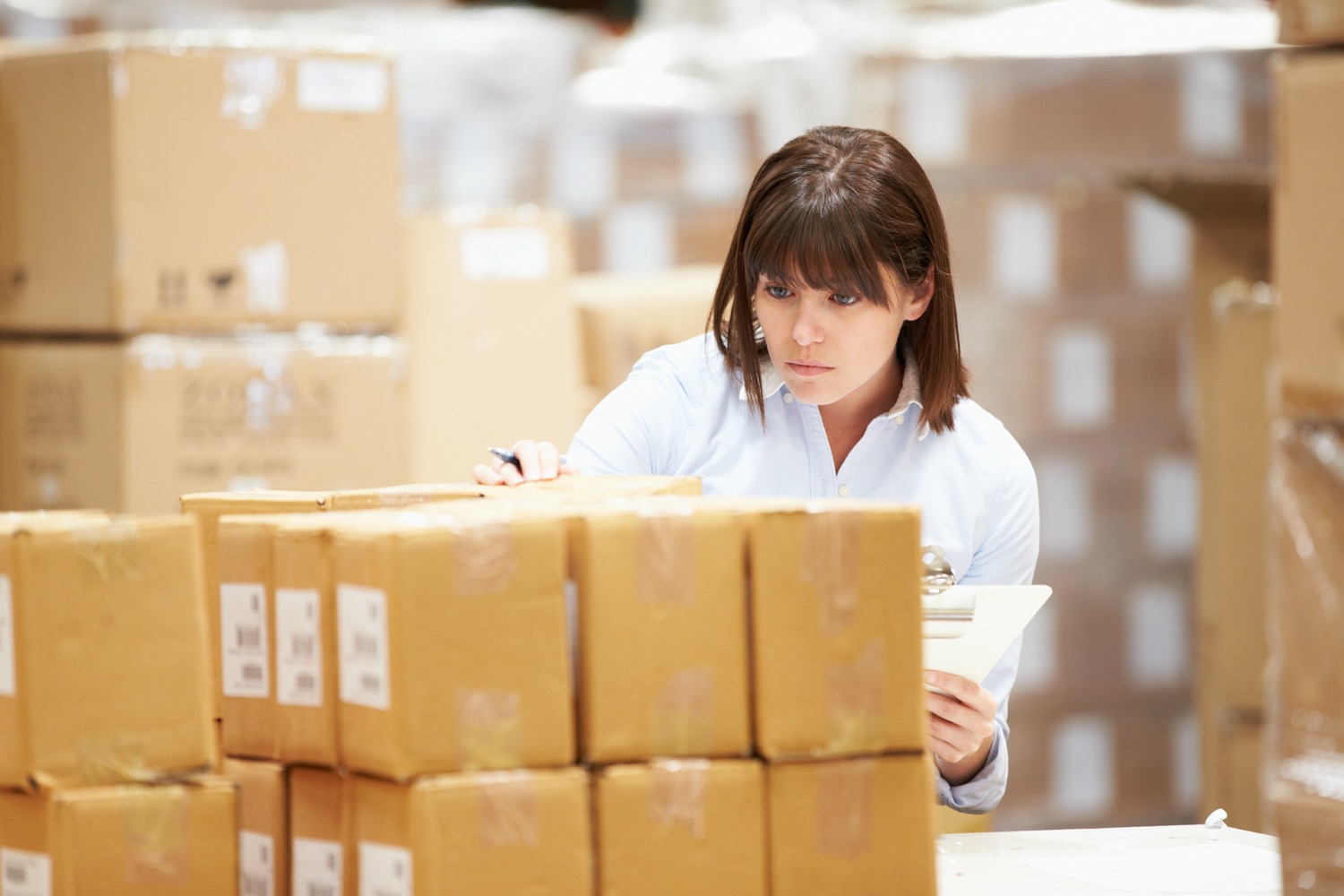
What is Advanced Planning Systems APS? To answer this question, it is necessary to say that this concept was developed through the joint efforts of scientists and software developers as a response to the limitations of classical ERP systems. Advanced Planning and Scheduling (APS) system is defined as any computer program that utilizes advanced mathematical algorithms and heuristic logic to perform optimization and/or simulation on finite capacity scheduling, job sequencing, resource allocation, capacity planning, resource planning, demand planning, and others.
An APS system can be a comprehensive package supporting planning processes at different levels as well as a specialized solution supporting a specific planning process. The definition of APS system also includes: 1) supporting planning in short-term, medium-term, and long-term periods, 2) creating and evaluating different scenarios, 3) evaluating constraints simultaneously, 4) using mathematical and heuristic algorithms to solve optimization problems.
Production planning and control tasks are important for most companies, so I want to delve further into the practical use of production planning and control systems.
APS systems provide analysis for the coordinated execution of supply, production, and logistics operations. They take into account the unique business rules and capacity constraints of each company and industry. APS systems represent the most critical technology of supply chain management. They create enterprise intelligence that supports planning activities at strategic, tactical, and operational levels and overall holistic decision-making process. So, what steps should you take to optimize production planning?
Improve Sales Forecasts
To create a production plan suitable for a variable supply chain or complex production process, data-based, evidence-based, and detailed forecasts are needed. Paper-pencil or Excel spreadsheets are now outdated and cumbersome methods that cannot meet the requirements. These methods have become obsolete to solve the details and complexity of a modern supply chain. Instead of traditional planning and scheduling methods, all touchpoints of the supply chain should be accessible to create advanced and analytics-based forecasts. Collecting data from all relevant touchpoints in the supply chain, followed by an effective S&OP (sales and operations planning), is the most effective first step that can be strengthened by this initiative. As a result of this effort, you can instantly visualize the results of different planning scenarios. The more accurate your initial forecasts are, the more your production planning ability will improve, and your optimization ability will strengthen.
Standardize Production Planning and Scheduling Processes
In addition to having an S&OP process, using comprehensive APS software that harmonizes demand expectations and capacity utilization is really helpful for manufacturers. This enables a significant balancing operation between demand and capacity. This operation can be seen as a type of formalization and provides indispensable benefits for production planning and scheduling processes. Questions like how long each stage of production actually takes, how long it takes to move raw materials from suppliers to the production floor, and how long it takes for finished products to reach the customer are quickly and accurately answered. Once these answers are obtained, all processes can be mapped end-to-end. After material flows, inbound and outbound shipments, and all production and logistics operations are effectively mapped, advanced planning and scheduling solution provides the insights needed to best execute the work. This minimizes total lead time and maximizes efficiency.
Use Digital Twins and Predictive Analytics
It should be ensured that robust decisions are made during the phase of creating a production plan. The stronger the forecasts, the stronger the production operations. At this stage of the production process, any adjustments that will increase the efficiency of the production process should be made. Among these adjustments are adjusting the layout of the factory, collecting materials in a planned and regular manner, and planning backup operations for possible machine failures. But which of these options is suitable for the production process? If advanced analytics and data collection methods are applied in compliance with the rules and regularly, a technology called digital twin used as a digital representation in the factory and supply chain enables the optimization of the production process. Through the digital twin, the expected/possible results can be visualized by producing simulations in desired quantities. Thus, the probabilities of the effects of a decision can be predicted, and even the best options can be reviewed in times of crisis.
Integrate Your Supply Chain
Due to the pandemic, constantly fluctuating supply chains are now slow and weak. Weaknesses in suppliers and shipping companies affect the ability to keep the right materials constantly at hand. Optimization can be done based on advanced analytics, but ultimately, supplier issues will create difficulties in obtaining necessary raw materials. This leads to delays in production and a decrease in the manufacturer’s profit margin and efficiency. For complete and robust optimization of the production plan, such problems should be anticipated and reduced. Not giving this opportunity to this probability and integrating the stages of the supply chain into planning is the most valid way to create an efficient production process. When data is integrated in real-time with the ERP ecosystem, it will be easier to perform risk analysis for these probabilities. With such an integration, risk analysis is included in the planning process. If data from supply chain partners can also be added to such an innovative workflow, a more robust planning function can be created.
Desire for Maximum Transparency
Transparency is the top priority of the supply chain. This is not only valid for this item but also for the previous ones. Production processes have now started to develop under new conditions, and this means that planning is done not with electronic tables and paper-pens but with real-time planning that provides a detailed and general view of the entire supply chain. Advanced Planning and Scheduling methods have now become indispensable for production processes. In the increasingly digitized and technologically advancing manufacturing sector, it is crucial to keep up with innovations and adapt. Insisting on the use of tools like Excel and similar spreadsheet tools will only be a waste of time and will lead to deficiencies in capacity planning. Real-time planning tools provide visibility and transparency for demand forecasts and capacity planning. This transparency is crucial for being able to respond quickly to disruptions like delays, maintaining the freshness of production plans, and ensuring smooth progress in the production process.
At Dijitalis, we are committed to solving complex planning problems. We explain how we handle and solve sample planning problems on our YouTube channel. You can watch our planning videos on our channel to learn more.