25 Recommendations for Efficient Warehouses
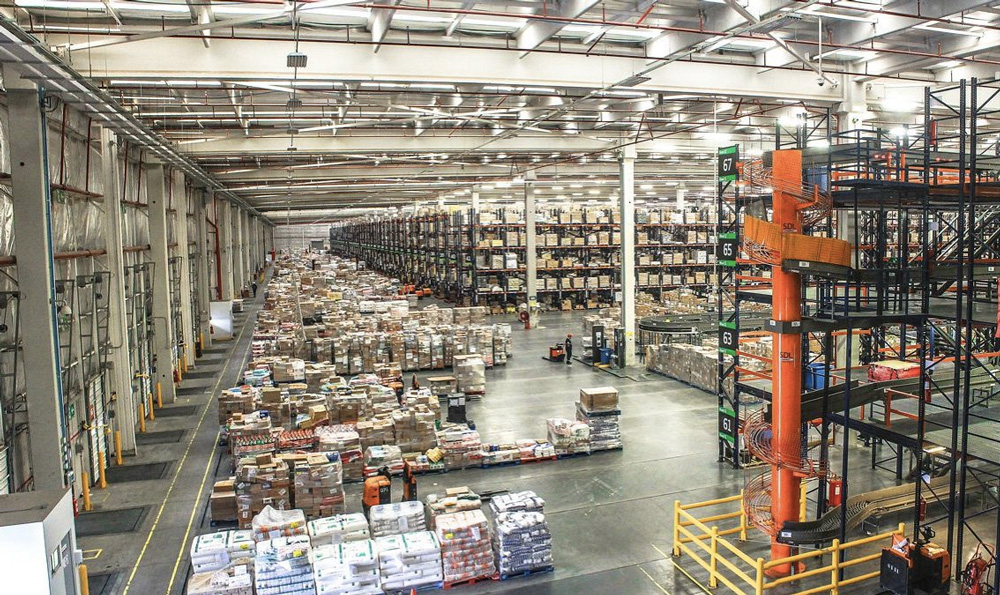
The concepts of modeling and simulation have been defined by the National Academy of Engineering and the National Research Council as a “technological breakthrough that deeply affects production performance.” If you are among the many SMEs aware of the critical analysis tool that simulation is for design and validation, that’s great! Because you are one step ahead of your competitors who still have insufficient awareness in the industry!
The simulation services we offer to SMEs as a low-cost, secure, and fast analysis tool are becoming increasingly important. The error-intolerant nature of the manufacturing process highlights the value of a qualified simulation, demonstrating how powerful it can be. Moreover, adopting a simulation approach in manufacturing, a critical point in the supply chain, is necessary to minimize the problems caused by fluctuations in the supply chain, respond quickly to needs, and provide flexibility.
Simulation Services
Simulation services have the capability to provide a data-based concrete solution. Shortening the product development cycle, perfecting your operations, and reducing the cost of bringing the product to life, no other tool can provide these services simultaneously. Considering today’s competitive market, all these services will enable you to establish a strong position in the market for your company and thus increase revenue.
The Importance of Simulation Methodology for SMEs
Meeting the demands required to improve performance and introduce new services is crucial. This is where simulation comes to your aid. Providing opportunities such as reducing costs and improving quality, simulation is exactly the service you need. One of the most important ways for SMEs to maintain their presence in the race is to seek help from advanced engineering tools like simulation.
Simulation offers a wide range of benefits, from strengthening collaboration with your customers, equipment providers, and supply chain partners to providing a preview of how a product will be produced. Thus, you can prepare a virtual view of the production facility for your customers and internal teams and demonstrate your value stream. Moreover, if you need to make a change in the flow, creating a new version is easier with simulation. Simulation eliminates the need for the old-fashioned trial-and-error method often required for changes in the manufacturing line setup.
Why Do We Need Modeling Methodology?
Simulation helps you test a system for an unlimited time and see how much you can push the system. This is not something easily done in a physical factory. The reasons for using simulation can be listed as follows for SMEs, regardless of the sector:
- Increasing system performance with Decision Support System (KDS),
- Activating the risk assessment method (What If Analysis),
- Providing the ability to deal with the complexities of variables and dynamic structures,
- Supporting focus on the smallest details.
Simulation with Analytical and Management Ability
Additionally, simulation will be your greatest ally in the analysis stage of your processes and in the following stages:
- Identifying factors causing system bottlenecks,
- Plant layout: Managing parameters of routing, stock, batch sizes, cycle times, and control systems for optimal layout,
- Changes in production: Inclusion of new products, changes in demand patterns, changes in product mix, changes in lead times, and production plan.
- Observing system performance: Efficiency, capacity, resource utilization rates, OEE.
- Observing resource utilization: Raw material usage, labor usage, machine usage, equipment usage.
- Analyzing various variables such as the expected performance of new or existing production facilities with simulation.
Problems Begin with Process, Time Constraints, and High Costs
The most common obstacles encountered in the implementation phase, which requires collaboration between departments and potential suppliers, are as follows:
- Time Consuming: The development phase of the simulation model is labor-intensive. Some complex simulation projects can take months to complete. This can be intimidating for SMEs. Nevertheless, many projects can be completed relatively quickly and with less effort. Allocating time to simulation services for a project involving critical tasks can save the company from significant expenses. Moreover, you can observe details with simulation that you didn’t notice before.
- Cost: Many simulation packages cost tens of thousands of dollars for a single license and require high-end computer hardware. These are all separate high costs. The company eventually has to choose between purchasing software or hiring an external consultant. Therefore, they benefit from ROI analysis.
The goal should be to make simulation a part of SME culture. Therefore, one of the points that companies building simulation models or consulting firms should pay attention to in order to effectively manage their projects is to have an employee trained in simulation within the company. Making simulation a culture in SMEs will create solutions for numerous problems and maximize benefits. The long-term usability of simulations is a unique advantage for improving your manufacturing operations.
- Project Management: Difficulties in understanding simulation still pose a major challenge today. Additionally, the confidence in simulation can still be shaky, which can lead to some difficulties. Senior management may have a general distrust of new methods or misunderstand the capabilities of simulation. While every scenario can be simulated, it would not be correct to say that simulation is the “best solution for all problems.”
- Technical Skills: Learning simulation methodologies and software is only part of what is required to be an effective modeler. The person modeling the simulation must create a model and interpret the results. They should be able to address issues in the model. Acquiring problem-solving and debugging skills is a time-consuming ability.
Review Operations in Detail
Simulation can be categorized among the basic needs of manufacturing companies today because it draws attention to details and develops a new perspective. Simulations document all the details. Moreover, it allows you to have more information about your operation. It enables you to see the interaction between operations that you might overlook in a spreadsheet or that may not be analyzable.
Yes, we can say that simulation has a high cost. However, it is worth considering that it will eliminate the extra expenses you will incur for the analyses you will need in the future. Like in any value creation process, investment, education, and time are required in using this service. If you already have a lean manufacturing project and engineering infrastructure, you may already be ready to use simulation. Thus, you will have a model ready to see the big picture in case of any disruption.
Most SMEs start with small projects on simulation systems. These are projects such as simulating a route, applying heat algorithms to see if a part will change shape, or if the part will wear out. Now you will be able to take on even more complex simulations. For example, you will determine whether to use conveyors or pallet trucks for material handling, and you will be able to improve your flow times and resource utilization rates.
Get in Touch Now
Many major manufacturers in the automotive and aviation sectors use simulation. However, High Mix, Low Volume (HMLV) SMEs, which are difficult to model due to their high diversity and low volume, may struggle to find the time and expertise needed to create and validate models.
Are you having trouble getting started with modeling and simulation applications? Dijitalis is ready to assist you with its expert team. Test your ideas before designing the facility of the future. Contact us today to start your project right away.