The top five sectors that will gain the most significant benefits from Digital Twin applications in 2021
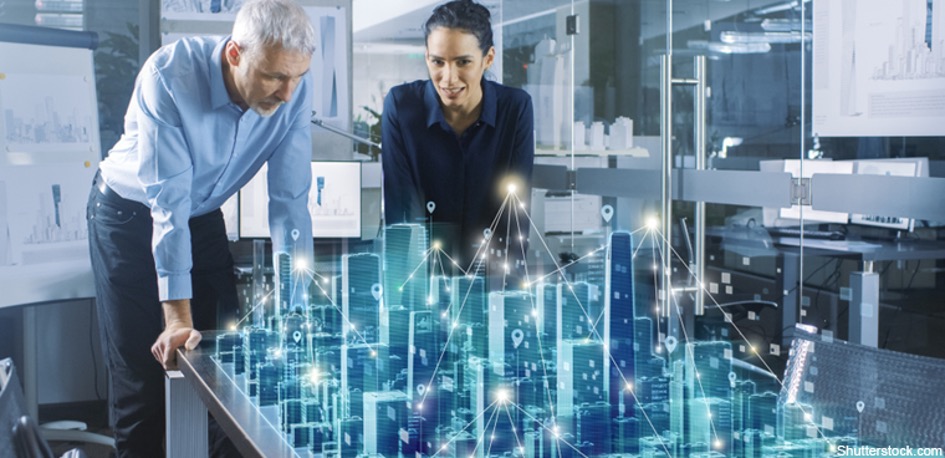
Digital twin usage areas can currently be listed as optimizing, monitoring, controlling, and automating industrial processes across various sectors. Statistics from 2020 reveal that the market size of digital twin technology is approximately $3.1 billion, with an estimated compound annual growth rate of 58%. This suggests that the market size will reach $48 billion by 2026. The projected growth rate is expected to be driven by the industrial adoption of digital twin examples. So, what are the top five industrial sectors that will leverage and reap the rewards from digital twin examples in 2021?
What is a Digital Twin in the Aerospace and Defense Industry?
In 2021, the aerospace and defense industry are expected to increase the use of digital twins as tools for industrial design, monitoring, process optimization, and security enhancement. The unique promise of digital twins is that companies in this sector can conduct comprehensive what-if experiments on digital copies of physical systems and processes without the need to worry about personnel safety.
At the industrial design level, Digital Twin technology is used as a tool for testing and evaluation to ensure the integrity of aircraft features and how they will function in the real world. For instance, evaluating the performance of wing flaps on jet engines, such as the thrust they produce in real-world environments. At the facility level, the aerospace and defense industry are expected to rely on digital twin technology or, in other words, digital twin technology for capacity planning, real-time remote monitoring, and process optimization.
Utilizing digital twins to monitor complex operational processes for providing accurate visualized data in real-time to aid decision-makers is an example. Digital twins can help rectify issues in operational processes with the 100% accuracy provided by a digital replica. Additionally, it provides remote monitoring support for stakeholders or analysts for facilities located in remote locations.
You can watch our video for real-life digital twin examples.
What is a Digital Twin in the Manufacturing Industry?
In the manufacturing field, digital twin examples can create a virtual model of an entire production process or system, such as an entire factory that collects data over the Internet of Things, in addition to a logical and mathematical model, also using virtual and augmented reality as well as 3D graphics and CAD models. This digital twin is a complete copy of the physical system existing in real life. The status of being a complete copy of a digital twin is maintained with real-time updates.
Digital twin examples of products can be applied to various environments, including monitoring products during use and throughout their entire product lifecycle.
The manufacturing industry has long led the successful implementation of digital twin technology. Digital twins have been applied in various ways in the manufacturing industry, such as optimizing manufacturing processes, supporting Industry 4.0 initiatives, providing optimized and data-driven performance, and serving as a remote monitoring tool. Due to Covid-19, which remains a significant factor, there have been major disruptions in production, traditional supply chains, and international distribution lines. Since most governments have implemented social distancing rules to protect workshop operators, these disruptions also affect the production area. These interruptions affect the production line and main production plans in various ways.
In manufacturing, you can use digital twin technology at various levels. These are, respectively;
Component level – focusing on a single and highly critical component in the production process.
Asset level – creating a digital twin of a single equipment part on a production line.
System level – using a digital twin to monitor and improve the entire production line.
Process level – this looks at the entire production process from product and process design and development to production and manufacturing. It is also valid for distributing and using the final product throughout the entire product lifecycle by customers/patients and also for developing future products.
Feasible strategies should be developed in 2021 to overcome both old and new hiccups in the manufacturing process. At this point, we predict witnessing the continuous implementation of digital twin technology. It is envisaged that digital twins will become a factory autopilot planning production processes according to existing resource capacity constraints and providing real-time operational support when things go off track. The increasing adoption of industrial IoT and computing is expected to provide the data necessary to create and continuously update the correct digital twins of the manufacturing process.
What is a Digital Twin in the Healthcare and Pharmaceutical Industry?
The healthcare sector is expected to be a significant adopter of digital twins in 2021 and beyond. The driving forces behind increased adoption also revolve around IoT, Industry 4.0, and patient care. The industry is expected to implement digital twin technology to collect data from patients, processes, and facilities to provide high-performance services to a broad and diverse customer base.
For patients, digital twins are observed to be used as a monitoring solution to map the effects of specific drugs on recipients. Data collected from implants and other medical technology devices also provide supporting information that the healthcare sector aims to use to improve both inpatient and outpatient services. The healthcare and pharmaceutical industry also expect to gain significant benefits at the facility level by leveraging digital twin technology‘s ability to accurately map complex processes. Thus, digital twins will be used as a capacity planning, inventory management, and remote monitoring tool to manage pharmaceutical product manufacturing and meet demand for large-scale vaccination products such as new coronavirus vaccines.
The use of digital twins or digital twin in the digitalization of medical products is also known. Here, digital twins are increasingly used to design and optimize medical distribution systems such as products and insulin pens. New pens are often designed from a digital platform, and then much of the design is reused in many different pen variants. With digital models, it is possible to quickly review whether a new variant fits into existing production equipment.
Additionally, many new additions have electronic functions that can tell a patient how to correctly use an insulin pen and send information about a treatment program to a doctor or hospital.
What is a Digital Twin in the Energy and Service Industry?
The energy sector is well-positioned to leverage digital technologies. Whether adding a vibration sensor to a rotating machine or creating a full digital twin of an entire facility, digital twin technologies, or in other words, digital twin can reduce costs and facilitate maintenance and operation processes.
Digital twins are a current topic, and many energy companies are eager to figure out how they can best benefit from their use. Most companies are looking for advice on where to start. Our advice is to start with good asset data you already have, get them into a shareable position, and grow from there. Often, good data is embedded in systems that the people who need it cannot access. One of the biggest advantages of digital twin technology is that it makes reliable, up-to-date information more widely available.
Also, delivering public services to tens of thousands of people in a city or millions of people in a geographical area is a complex process that public service providers continue to struggle with. For example, in the energy or electricity sector, the ability to predict power outages and determine how much of a power grid’s physical and cyber control systems remain active during a power outage or natural disaster is crucial. At this point, digital twin technology plays a significant role in predicting how quickly energy sources will react.
Managers in the energy and utilities industry regard digital twin as a powerful tool to develop a more robust and manageable network. Real-time data exchange between the power grid system and auxiliary systems such as digital twin technology facilitates the identification of the effects of external factors on the grid. This data exchange also indicates that measures to prevent the grid from collapsing can be taken in advance, and the duration of potential power outages will decrease. The energy and public utilities sector are expected to use digital twins as a monitoring, predictive, and analytical tool to provide optimized services to their customers in 2021.
What is a Digital Twin in the Transportation Industry?
Capacity planning for logistics resources (warehouses, distribution fleets, etc.), scheduling of warehouse docks, route optimization for last-mile vehicles, and tracking all assets are the lifeblood of the transportation industry. Digital twin provides the most advanced technology that can perform all these activities to ensure the optimum operation of airports, trains, and urban transport facilities. It is expected that digital twin technology will utilize data captured by comprehensive IoT networks to optimize various processes in the transportation industry. Digital twin will assist in capacity planning, scheduling, and monitoring the progress of transportation assets in the logistics sector as a whole, train stations, or airports.
In conclusion;
Digital twin technology is a powerful analytical tool that all sector-independent product and service providers should seriously consider in 2021. By requesting a demo of our Digital Twin solutions, you can learn more about how digital twins work in your industry or specifically within your own organization, and concrete applications.