Tips for Proper Inventory Management
Chapter I: Finished Product Inventory
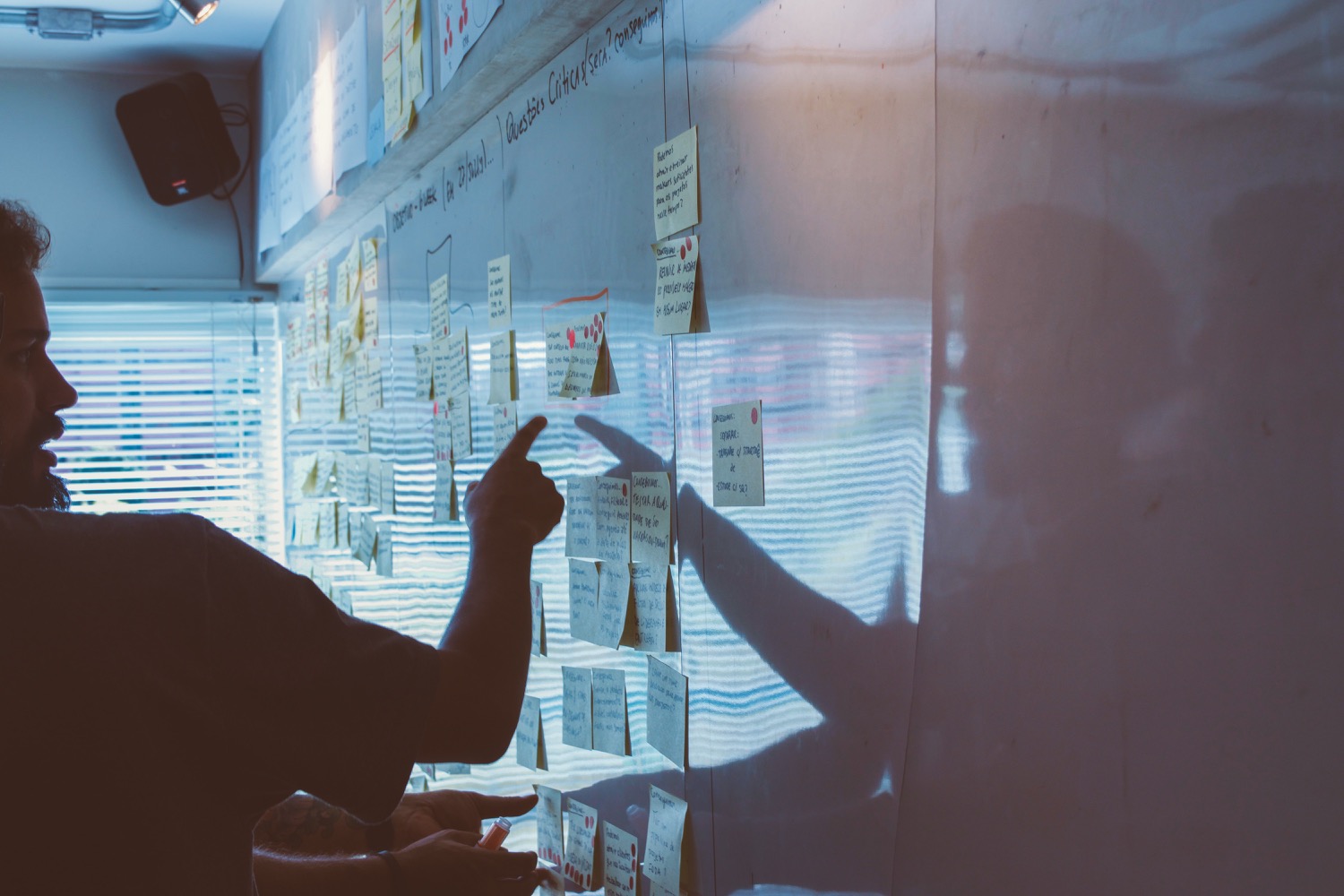
Inventory management is essentially a subject that needs to be examined in two dimensions. On one dimension, it involves the management of raw materials or semi-finished goods, while on the other dimension, it involves the management of finished product inventory. In this article, I will attempt to provide insights into finished product inventory management.
What is finished product inventory?
All manufacturing and marketing companies have finished product inventories at various points along the entire supply chain. As products move through the supply chain from the production point to the end customer, depending on the sales and delivery model, inventory ownership can be held by the main manufacturer or by intermediaries associated with sales channels (such as trading partners, distributors, and dealers, etc.).
Why and when do organizations maintain finished goods inventories?
Organizations conduct detailed analysis of both national and international/global markets and optimize the location of production facilities, necessary warehouse networks, and their numbers according to supply chain strategies. The goal here is to achieve high customer satisfaction and demand fulfillment rates by keeping important parameters such as carrier, inventory holding plan, shipping lead times, and order management delivery times in mind while delivering products to domestic and international markets. The biggest problem we have encountered in inventory management in companies so far is usually not knowing where, when, and in what quantity to keep the product.
When making decisions, companies usually make very simple calculations; taking averages, planning based on previous or last few years’ sales volumes can seriously mislead you. The cost of this misconception comes back as high costs. Some companies are not even aware of these costs. They constantly try to rush products from places where they should not be to places where they should be with extra shipping costs.
The solution to this problem can be found with scientific approaches such as inventory optimization. In fact, even without the need for these techniques, basic calculations such as simple regression analyses, correlation of product and marketing strategy, sales frequency, etc., can minimize errors. Considering that companies classified as corporate set their delivery times within 48 hours or 24 hours, how important these calculations are can be more explanatory.
Production strategy may require inventory holding!
Companies trying to apply the zero stock principle in assembly lines to the entire supply chain are in a big misconception. Production and inventory strategy are directly related to marketing strategy. Accordingly, production is planned according to production-to-stock or production-to-order strategies. The production-to-order creation strategy produces based on specific orders and does not guarantee the holding of stocks other than transit stocks, while the production-to-stock type of production ensures the holding of inventories in various distribution centers and transfer centers to meet market demands.
Market Penetration
The marketing departments of companies often run branding and sales promotion campaigns to increase brand awareness and create demand. An aggressive market penetration strategy depends on the presence of inventory of all products at the nearest storage location so that the product can be delivered within a short time, within hours, at all sales locations across the region and city. The absence of any stock at the point of sale will result in a decrease in market demand and sales. In fact, the sales opportunity will be missed. Therefore, holding inventory becomes a necessity.
Market Size, Location, and Supply Design
Supply chain design takes into account the location of the market, market size, demand model, and transit delivery times required to deliver stocks to the market, and determines the optimal inventory levels and distribution network locations to hold inventories at national, regional, and local levels. The primary objective will be to ensure the availability of the correct product stock to serve the market. Secondly, stocks are held in required locations, and unwanted stock accumulation is prevented.
Transportation and Physical Barriers
When the marketplace and the physical area of the market are combined with the local truck and transportation network, inventory holding is often demanded at the nearest locations. For example, mountainous areas may require longer delivery times for service. The desired vehicles may not be available, and you may have to rent large-capacity special container vehicles. In such cases, an inventory holding plan for such markets will be necessary. This is one of the biggest mistakes made when determining the location of the distribution center. A distribution network designed solely based on coordinates on a map and sales locations may indicate an area miles away from civilization, such as a mountain peak or forest interior.
Distant marketplaces mean longer delivery times and transportation delays. The inventory holding policy will take these factors into account when making the plan.
Local tax and incentives are rules set by regional management
Accordingly, while one city may offer incentives such as tax refunds for a certain product category group or organized industrial zone, another city may demand higher local incentives and lower inter-city taxes. In such cases, demand for a product from a neighboring state may increase according to the local province. Accordingly, inventory holding should be planned to meet market fluctuations. To elaborate a little more on this; from a project we conducted, shipments from a distribution center in Moscow to a customer on the western border of Russia were provided under more favorable conditions when made from Poland, despite being within Russian borders.
When exporting to another country from the country of origin, rules regarding import and customs duties must be considered to decide whether inventories will be held on the way or at the destination.
Providing production lead times (On-time readiness)
In cases where the lead time for production is long, safety inventory holding becomes necessary. In such cases, sudden market demand or opportunities require the creation of safety inventories and, accordingly, affect the procurement of material stocks.
Speculative gains
Companies always monitor the economy, annual government budget, financial environment, and international environment and can predict situations that may affect their business and sales in advance. When they can predict a change that will cause a general increase in sector prices, taxes, or other levies, they tend to buy and hold large stocks of raw materials at current prices. They also hold finished product stocks in warehouses in anticipation of an upcoming price increase. All these movements cause companies to hold more inventory at various stages.
Avoid certain costs
Finally, companies create safety inventories to meet customer demand, fulfill sales, reduce order costs, reduce inventory and transportation costs, and reduce delivery times. Some companies strengthen their distribution networks and design logistic infrastructures that include high-frequency low-volume direct shipments from production points to reduce costs. While it is possible to implement these logistic infrastructures, a successful design can only be achieved through the simultaneous alignment of different processes such as strong demand planning, production planning, decision-making in sales and marketing strategies, carrier compliance, and customer management.
Thanks to our powerful optimization software and experienced project team at Dijitalis, we can design a supply chain optimization along with the inventory management system mentioned in this article that will work with the optimal network and logistic infrastructure.