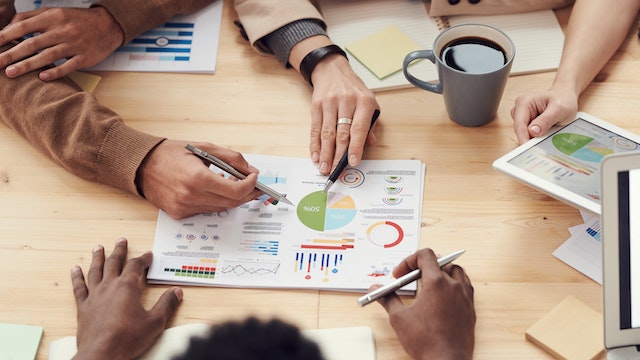
When we look at it conceptually, minimum consistent and sustainable data are needed to be able to do operational planning. The difference between consistent and accurate is striking here. Without delving too much into statistical concepts and machine learning theories, it can be said that relatively little variation among the data in the dataset indicates that the data is relatively consistent within itself, but it is not sufficient to conclude that the data is accurate. Although we often complain about the lack of accurate data in business life, the main issue is actually the inconsistency of the data, and generally, the inconsistency of the data is the biggest obstacle to planning.
The other requirement is the necessity of obtaining the desired data at the desired frequency, which reduces the percentage of reflecting reality in the schedule disruption plan and reduces its reliability.
From this perspective, it is necessary to continuously measure the quality of the data that feeds into the system and to monitor it in a way that the user can understand, with pre-designed performance indicators. In this regard, companies developing planning solutions should spend a lot of time, especially on notification management.
Asprova, one of the leading software in detailed scheduling, enables users to interpret the current situation quickly and make better decisions with its different scheduling options and visually rich screens.
For example, with the Resource Gantt chart, it is possible to determine how late orders are, why they are late due to which operation and machine, and bottlenecks can be identified accordingly. Especially with the precedence-successor relationship between operations in this chart, scheduling of a part to be assembled, for example, is prevented before its subparts are ready. Accordingly, the upper product to be scheduled ahead without its subparts ready cannot be scheduled ahead. Similarly, in order not to create unnecessary inventory costs, other sub-parts dependent on the upper product with one sub-part missing are not produced unnecessarily or even prematurely, and intermediate stock levels are not raised above the specified stock level.
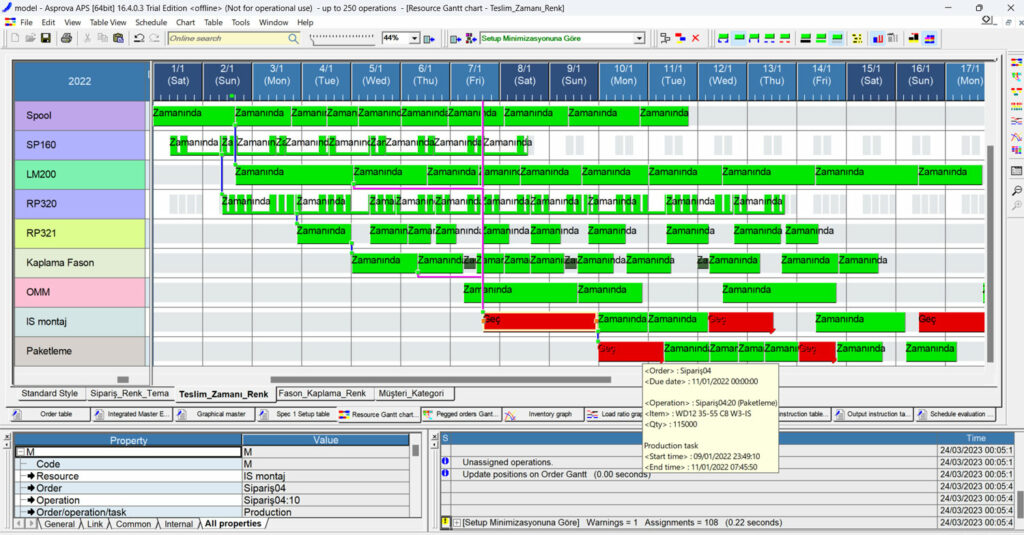
In addition to detailed scheduling on order, product, and machine basis, information is shared with the user regarding the general situation of scenarios.
The user examining the following warning window should repeatedly check the order quantities entered into the system and the delivery dates. Excessive tight deadlines can increase costs. Besides, it should be considered that if the share of setup time exceeds 15% of the total time, and nearly 50% of the total production time in a 3-operation production model consists of valueless waiting time. Here, both standard warning mechanisms and warning templates that can be customized according to user preferences allow continuous control of system data and their relationships can be monitored.
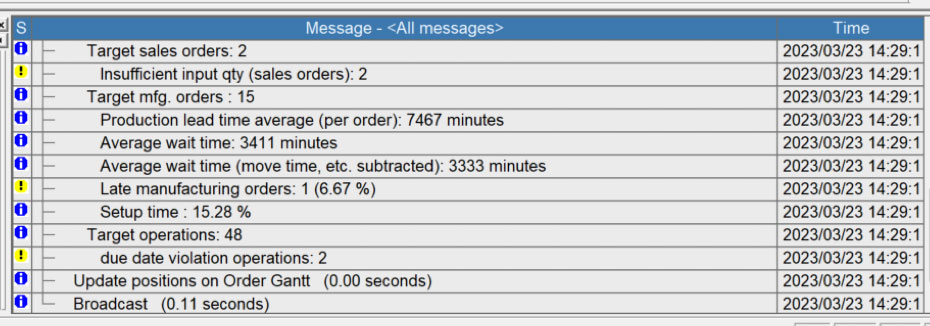
On the other hand, while the normal operation flow continues, we may want to run different scenarios by simulating possible situations by making changes in the operational dataset and/or planning policies and methods.
For example, in the following scenario, 13 different scenarios and their results can be compared before they actually happen, and actions can be taken according to the desired performance indicators. Here, comparisons are made based on three different order priorities.
To go deeper, in scenario 11, the breakdown of a bottleneck machine is examined, and then options such as shift opening, closing scenarios, options for producing the part in alternative machines and production lines, and options for increasing/decreasing operators on the assembly line are evaluated to minimize the losses in this scenario.
As a result of all these trial and error processes, different scenarios are crossed, and the number of delayed orders is reduced to zero.
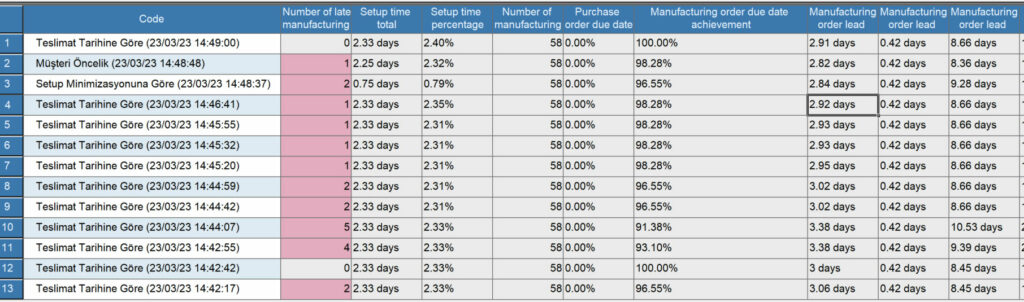
Here, with proactive data control, visual warning systems, and multi-scenario management that we have emphasized with examples, detailed operational schedules can be created and dynamically updated according to changing or potential situations.