Eliminate Bottlenecks in Production
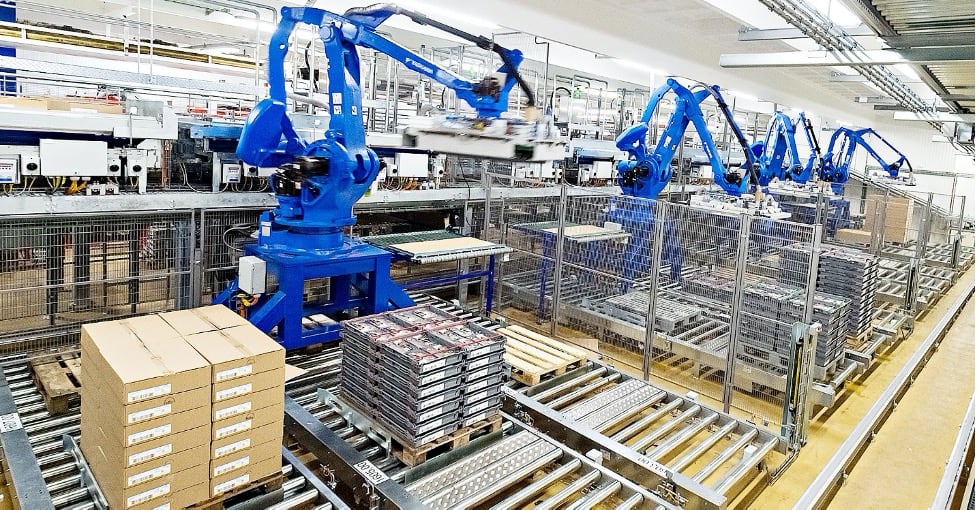
Today, many companies hesitant to make mistakes are testing the “future state scenario” they will reach after making new investments in their factories by conducting digital factory simulations before investing. By conducting simulation-based investment analysis, you can identify and eliminate potential problems you may encounter in the future.
In a case study, our clients sought consultancy from us regarding expanding their factory. Since the investment in the existing factory was substantial, all decisions needed to be carefully analyzed. Dijitalis supported its work in designing the future state of the facility with digital factory simulation.
For businesses, production simulation means creating a realistic virtual copy of factory investment and layout plans.
Our client provided information about the expansion plan to increase capacity. We created a scenario using both this data and past production statistics, adding product, machinery, and inventory data to it. Based on these results, we built a three-dimensional model of the planned operation and began testing various scenarios on this model.
Such production simulations are conducted to see if everything will go as planned and to understand which details need to be altered.
Through digital factory simulation, our client also measured whether the entire automation infrastructure, such as robots and conveyors, would cause any problems. This test also identifies bottlenecks that would slow down the process. Additionally, it determines how the factory design can be redesigned to increase efficiency.
As a result of digital factory simulation, our client had the opportunity to improve their plans. For example, bottlenecks caused by insufficient equipment were identified. The optimal number of equipment to address this issue was calculated. Similarly, it was measured that the desired efficiency could be achieved by removing some equipment from the investment plan. Thus, the targeted capacity can be reached with a lower investment budget.
Our client was able to measure which types of equipment, other than those they currently use, could work more efficiently based on the digital factory simulation we created.
The increasing popularity of production simulations is the best solution that businesses can use to compete better and strengthen financially.
More and more companies are using simulations to experiment before implementing decisions.
Conducting these simulations also speeds up the planning process. Because possible problems and methods that can be used to accelerate tasks can be tested. These simulations can also be used for different operations such as production and packaging. Digital factory simulation can be applied to all processes such as product flows and the use of robots.
Three-dimensional visualization included in production simulation is becoming increasingly realistic. Computers are evolving day by day, allowing you to see details firsthand and experience a more interactive virtual reality.
Simulation software will be able to dynamically use management systems and machines by receiving data from them in the future. This shows us that shorter-term plans, such as detailed scheduling, may be more detailed and realistic through simulation. The results will be revolutionary because production systems are becoming increasingly complex. The more varied the product trees and material routes are in a production site, the more difficult the processes are to define, or if risks related to implementation need to be minimized, dynamic production simulations become even more critical. We now call simulation models that autonomously exchange data with ERP and MES systems and make decisions dynamic outputs digital twins.
Digital factory simulation can be described as a risk-free and cost-effective laboratory that allows you to test any critical decisions related to the factory in advance.