What is APS (Advanced Planning System)?
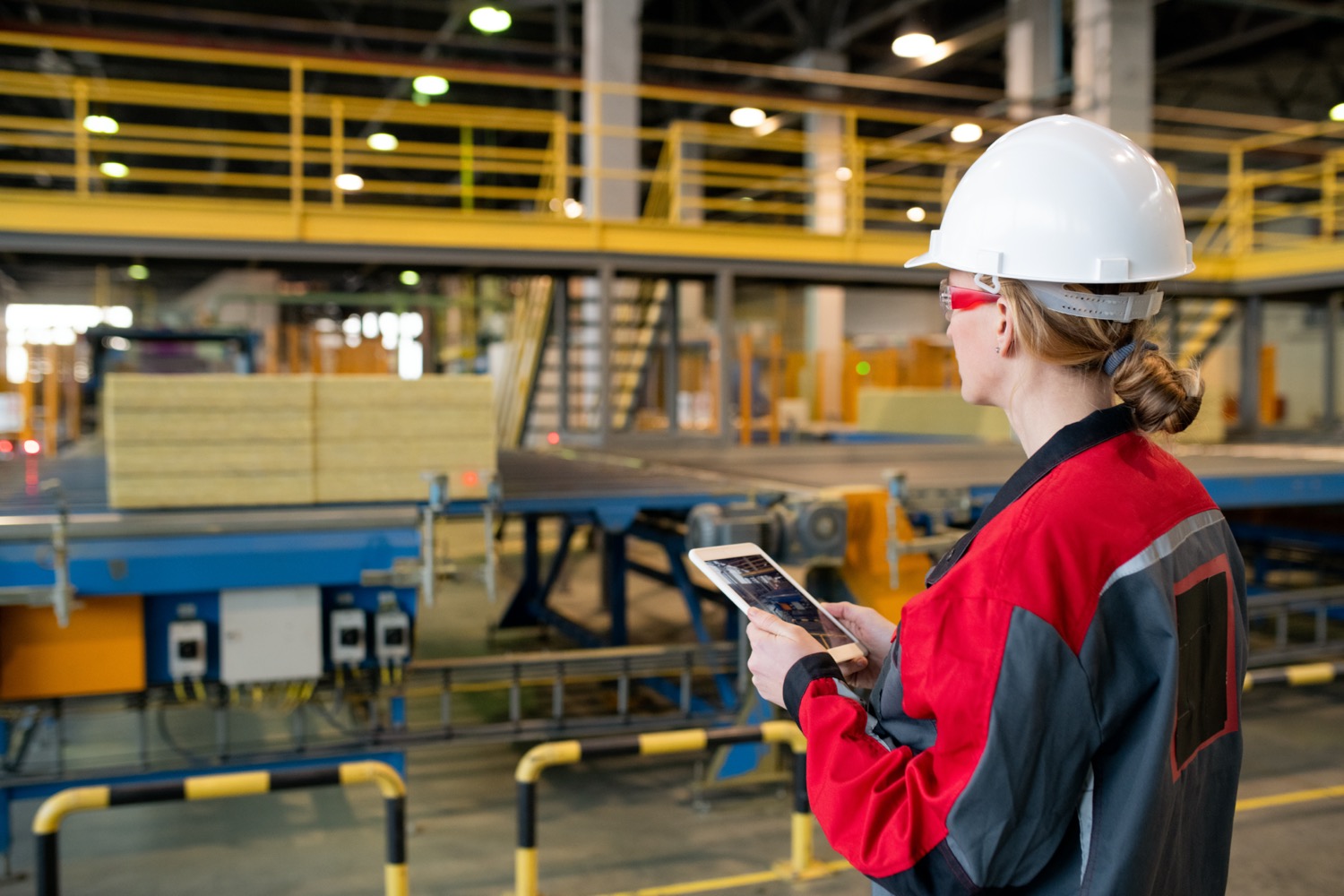
In today’s conditions, manufacturers must have an advantage against competition. Factories are constantly seeking ways to be more efficient and to be the top player in the market. From our perspective, a factory that does not use an advanced planning system (APS) cannot fully achieve this goal. Advanced planning systems (APS) are designed to improve the synchronization of production processes, provide foresight by predicting the future, increase capacity utilization and on-time delivery rates, and also reduce inventory levels and waste simultaneously.
How Advanced Planning Systems Work?
Planners spend their time constantly struggling with Excel spreadsheets under pressure to create a production schedule. However, even when these schedules are published to the production floor, they may become invalid. Many things may have happened on the production floor during the scheduling process; such as machine breakdowns, labor shortages, delayed supplier shipments, and so on. While this situation can be demoralizing, it is the inevitable nature of the manufacturing world. Since we cannot change this, we must find a way to reduce the effort spent creating or revising the schedule. APS solutions not only shorten the planning time but also allow for numerous scenario tests such as impact analysis.
Creating a feasible production schedule is not an easy task. There are many parameters to consider. The feasibility of a schedule depends on how much it can be reflected within the APS. For example, machines, labor, molds, equipment, and materials have finite capacity and must be evaluated as such. Often, it is not sufficient to produce just one schedule; separate what-if scenarios may need to be simulated for each goal, such as minimizing costs, reducing production times, and working with minimum inventory. A robust APS solution can provide these capabilities and seamlessly integrate with other IT systems (ERP, MRP, MES, etc.) to continuously update its schedule based on current data.
The Real Benefits of Advanced Planning Systems
To summarize these benefits qualitatively, with a planning and scheduling tool truly equipped with APS features, devised by expert consultants, the following benefits can be obtained:
- Visibility: Being able to track each job order and preempt potential problems
- On-time Delivery: Meeting customer demand with realistic calculations instead of speculative forecasts
- Inventory: Minimizing in-process inventory, shortening production times
- Profitability: Maximizing capacity utilization, reducing wait times, improving productivity to strengthen cash flow
When you create an up-to-date and accurate schedule, you achieve ongoing and escalating productivity throughout your production processes. When you can foresee the future of the production floor, you make more accurate decisions with less stress. You also provide significant performance improvements that affect the factory’s balance sheet in response to every setback and change.
Quantitatively speaking, in the projects we’ve undertaken, we’ve measured the following results on average:
To read the success story and user interview of our finite capacity planning and detailed scheduling project in an automotive subcontractor factory, please contact us at success@dijitalis.com.
What is the Difference Between Planning and Scheduling?
The most fundamental difference between planning software and scheduling software is that planning systems plan with time buckets (monthly, weekly, daily) and do not sequence operations into buckets. Real scheduling systems, on the other hand (you should be wary of those that do not really do this but only seem to), do not use time buckets; they sequence operations according to certain objectives. Assigning each operation to an appropriate production resource is essential for achieving operational efficiency and optimizing system performance. Detailed scheduling software plans a closer future and considers process routes with production rules much more detailedly compared to planning systems.
Planning software combines sales forecasts and long-term orders, matches targeted stock levels and grouped resource capacities to meet demand. Planning can be done in finite or infinite capacity mode, and the planning horizon can be in terms of days, weeks, or months. When used in conjunction with scheduling system, the output of a detailed production schedule is fed back into the planning system for revising planned production quantities with those scheduled. As a result of this iteration, a master production schedule is calculated.
Scheduling software are finite capacity tools that work on a detailed model of the factory. They take into account the real availability of resources and produce a feasible schedule by evaluating numerous production constraints. The scheduling activity is generally used by manufacturers who feel the need to manage machines and production lines very well, as well as in service and logistics sectors. Typically, the input to scheduling is production orders, and each order competes along the production route to access available resources. The rules of this competition are defined by sequencing strategies specified in the model. The schedule is visualized with a Gantt chart, and a production list is published for each production resource.
To see how we solve sample scheduling problems, you can check out our YouTube channel.